The rotor of a screw pump is a central component within a screw pump, usually consisting of one or more helical shafts. A screw pump, also known as a screw pump, is a type of pump that uses a helix on one or more rotating shafts to move liquids or viscous fluids. This type of pump consists of two main parts: the screw pump rotor and stator.
In a screw pump, the rotors are those parts with a helical profile that are mounted on the pump shaft. As the rotor rotates within the stator, its helical shape forms continuous sealing chambers with the inner cavity of the stator. As the rotor rotates, these chambers move along the pump from inlet to outlet. Because the volume of the chambers remains constant as they move, progressive cavity pumps can transport viscous fluids with little or no pulsation.
The design of the rotors in a progressive cavity pump directly affects the efficiency, flow rate and pressure of the pump. They are usually made of wear-resistant materials such as stainless steel or specially treated metals to resist abrasion or chemical corrosion that may be present in the fluid. Screw pumps are widely used in the chemical, petroleum, food processing and wastewater treatment industries due to their smooth delivery, low noise levels and ability to transport fluids containing solid particles.
Why are screw pump rotors so important?
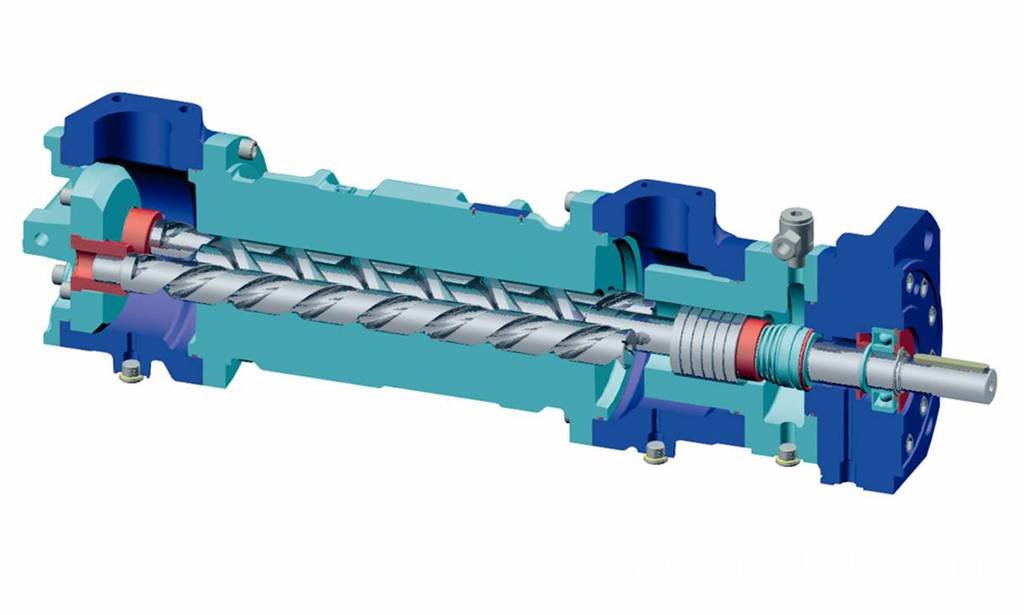
Screw pump rotor plays a key role in the overall operation of the pump. I will explain its importance to you below:
- The core component of a screw pump: The core component of a screw pump is a screw assembly consisting of one or more rotors. The shape and size of the rotor determines the flow and pressure characteristics of the pump.
- Conveying medium: Screw pumps make use of the relative motion between the rotors to form a closed volume between the screws through the rotation of the screws, thus realising the conveying of liquid or gaseous medium.
- Improve efficiency: High-quality rotor can significantly improve the efficiency of the pump. This is because excessive energy losses during operation are avoided and friction damage, which can cause early equipment failure, is reduced.
- Withstand pressure: the rotor is located between the screw sleeve has a high volumetric efficiency, can withstand high pressure, so the screw pump is also widely used in high pressure environment.
- Impact on equipment life: The quality of the rotor also has a direct impact on the stability and life of the overall pump. Inaccuracy or rough surface of the rotor may increase the vibration and noise during operation, accelerate the wear of parts, and thus shorten the service life of the equipment.
In order to ensure the normal operation of the screw pump, manufacturers will invest a lot of energy and resources to manufacture and inspect the rotor, in order to achieve the highest technical standards and quality requirements.
Common screw pump rotor types and application
Screw pumps can be classified into various types according to the number and shape of rotors, and they are each suitable for different working conditions and application scenarios. The following are some common types of screw pump rotors and their applications:
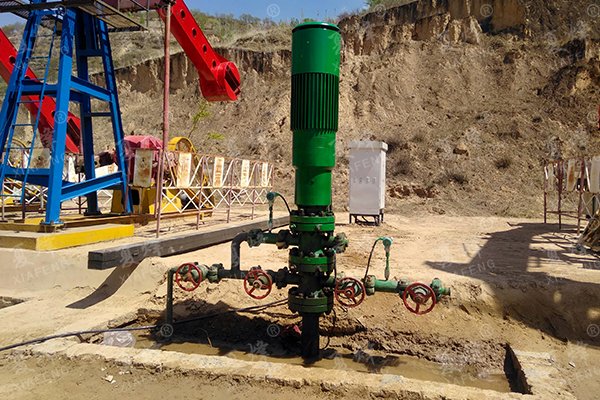
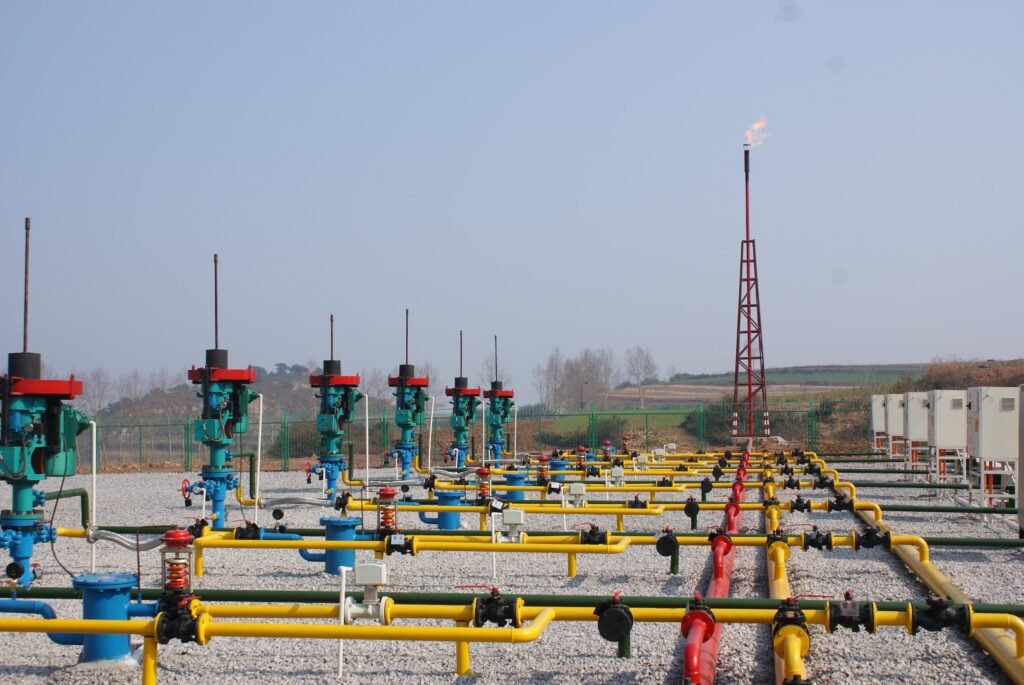
Single screw pump (single rotor pump): this type has only one rotor. It is typically used for conveying viscous and solid-containing media, such as wastewater treatment, food processing and chemical delivery.
Twin-screw pumps (double rotor pumps): Twin-screw pumps have two intermeshing rotors. Depending on the shape of the rotor heads, they can be further classified as symmetrical and asymmetrical rotors. Twin-screw pumps are used in the oil and gas industry, the chemical industry and the shipbuilding industry and are particularly suitable for conveying clean or slightly contaminated low to high viscosity media, as well as multi-phase mixtures.
Three-screw pumps (triple-rotor pumps): contain three rotors, one of which is the driving rotor and the other two are the driven rotors. This type of pump is widely used in ships, power generation, heavy industry, and hydraulic systems for its highly smooth operation and good high-pressure performance, mainly for the transport of clean, low-viscosity oils or similar liquids.
Five Screw Pumps (Multi-Rotor Pumps): This is a more advanced type of screw pump with five or more rotors that provide extremely high pressure and flow stability. This type of pump is used in application scenarios that require very high pressure and flow control, such as large industrial systems, high-speed train lubrication systems, etc.
Special designs of progressive cavity pumps: In addition to the standard types mentioned above, there are also special designs of progressive cavity pumps, such as variable pitch pumps, wide groove pumps, etc., which are optimised for certain specific application scenarios, such as extreme viscosity conditions, non-conventional fluid properties etc.
Each type of screw pump rotor design has its own unique characteristics and advantages, should be based on the specific characteristics of the transport medium and application requirements to select the appropriate type of pump.
screw pump rotor machining methods
Several machining methods are used for the production of screw pump rotors, each having its own advantages and ideal use cases. Among these methods, whirling, a process earlier discussed, stands out for its efficiency and precision, especially for complex shapes like those seen in screw pump rotors. Below, I’ll describe common methods used in machining screw pump rotors and highlight the applicability of thread whirling.
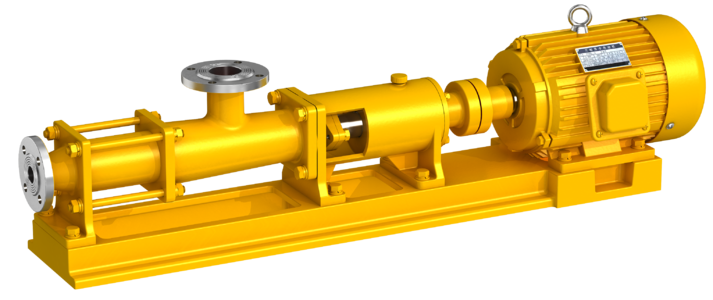
Turning: Traditionally, turning has been a primary method for machining rotors. It involves rotating the workpiece (the rotor blank) on a lathe while a cutting tool removes material to achieve the desired shape. However, turning can be limited in precision and efficiency when dealing with the complex, helical geometries of screw pump rotors.
Milling: Milling involves the use of rotary cutters to remove material from a workpiece. For screw pump rotors, specialized CNC milling machines can be programmed to achieve the intricate helical geometries required. While precise, milling can be time-consuming and may require multiple setup changes for complex parts.
Grinding: Grinding uses an abrasive wheel as the cutting tool, providing very high precision and surface finish. For screw pump rotors, profile grinding is especially useful for fine-tuning the rotor’s geometry and improving its surface quality. However, grinding can be slower and more costly than other methods.
Thread whirling: Thread whirling is a specialized machining process designed specifically for producing helical components, such as screw pump rotors. It involves rotating the tool and the workpiece in opposite directions, allowing for the precise and efficient removal of material following the helical path. This method is highly efficient for the complex geometries of screw pump rotors because it combines the cutting speed and precision needed to produce these components effectively. Whirling can significantly reduce machining time, improve surface finish, and extend tool life compared to traditional methods.
In summary, while traditional methods like turning, milling, and grinding are still used in the production of screw pump rotors, whirling offers a specialized, efficient, and precise approach ideal for the complex geometries of these components. The choice of method ultimately depends on the specific requirements of the rotor, including the precision of the geometry, the desired surface finish, and production efficiency.
Advantages of thread whirling for machining screw pump rotors
Thread whirling, compared to other machining methods, offers several distinct advantages, especially when it comes to manufacturing components with complex geometries like screw pump rotors:
Precision in Complex Shapes: Whirling is highly precise and can produce complex helical shapes and intricate profiles that might be challenging or time-consuming with conventional turning, milling, or grinding methods.
Efficiency: The whirling process is generally faster because it allows for the simultaneous cutting of multiple threads or grooves. It can complete a part in fewer passes, reducing the overall production time.
Tool Life: The cutting forces in whirling are distributed evenly across the cutting tool, leading to reduced tool wear and increased tool life. This can save costs on tool replacement and downtime for tool changes.
Surface Finish: Whirling can achieve a high-quality surface finish, often eliminating the need for secondary finishing processes like grinding.
Vibration Reduction: The whirling process can reduce vibrations due to the synchronization of the rotation of the cutter and the workpiece, contributing to a better surface finish and higher precision.
Material Flexibility: It can machine a wide range of materials, including hard-to-cut materials, due to the potential use of multiple cutting edges and the ability to control cutting speed and feed rate.
Cost-Effectiveness: With its ability to accurately machine complex geometries in a single setup, whirling can reduce the cost of production by minimizing the need for multiple machine operations and setups.
When it comes to screw pump rotor machining, the specialized nature of the whirling process matches the product’s demands for precision and efficiency, making it an advantageous method over other more traditional machining techniques.
The key influences on the machining quality of screw pump rotors
he quality of machining screw pump rotors is influenced by several critical factors:
Machine Tool Accuracy: The precision of the machine tool used for machining directly affects the accuracy of the rotor profile. Advanced CNC machines with high positional accuracy are essential for producing tight-tolerance components.
Cutter Quality: The quality of the cutting tool, including its material, geometry, and coating, plays a significant role. High-quality cutters can produce accurate profiles and fine surface finishes while minimizing wear and tear.
Cutting Parameters: This includes the cutting speed, feed rate, and depth of cut. Optimizing these parameters is crucial for achieving the desired surface finish and dimensional accuracy, as well as prolonging tool life.
Workpiece Material: The material properties, such as hardness, strength, and ductility, impact how the machining process should be approached. Selecting the appropriate tooling and machining parameters for the material is vital.
Coolant and Lubrication: Proper cooling and lubrication reduce heat and friction, preventing material deformation and ensuring a better surface finish.
Operator Skill: Skilled operators with a good understanding of the machining process can make adjustments to compensate for tool wear and variations in the workpiece material.
Tool Path and Machining Strategy: The programming of the tool path, including the selection of the right type of tool movements and sequences, affects the overall machining time, surface quality, and accuracy of the rotor profile.
Machining Environment: Environmental factors such as temperature and humidity can cause material expansion or contraction, potentially affecting the dimensions and tolerances of the machined rotor.
Measurement and Inspection: Regular inspections using precision measuring instruments are necessary to ensure that the rotor dimensions are within the required tolerances. Feedback from inspection results can be used to adjust the machining process in real-time.
Machine Maintenance: Routine maintenance ensures that all parts of the machine are working correctly and efficiently, which is essential for maintaining the quality of the rotor over time.
Machining screw pump rotors to high-quality standards requires a combination of the right equipment, cutting tools, skilled operation, and strict quality control measures. Each of the factors mentioned above must be carefully managed to produce rotors that meet the required specifications and performance criteria.
How Continuous Improvement and Innovation in Rotor Machining for Screw Pumps Can Improve Pump Reliability?
Continuous improvement and innovation in the machining of screw pump rotors directly impact the reliability of the pumps in several key ways:
Enhanced Precision: Innovations in CNC technology and other machining processes enable the production of rotors with extremely tight tolerances. This elevated precision leads to better fitment between the rotors and the casing, reducing leakage and improving efficiency, ultimately enhancing the pump’s reliability.
Improved Material Usage: Advanced machining techniques can handle a wider range of materials, including those with superior wear properties. By using more durable materials that are resistant to corrosion and wear, the longevity and reliability of the pumps are improved.
Superior Surface Finishes: Continuous improvements in cutting tool materials and coolant technology result in smoother surface finishes. This reduces friction between moving parts, lowers the risk of contamination, and minimizes the rate of wear, all contributing to the pump’s reliability.
Consistency in Manufacturing: Refinements in automation and quality control ensure that each rotor is consistent with the next. This uniformity is crucial for mass-produced pumps, as it assures users that every unit they purchase will perform as expected.
Thermal Deformation Control: Innovations in machining, such as cryogenic cooling, mitigate thermal deformation during the manufacturing process. By maintaining the integrity of the rotor dimensions, the pump operates more reliably over a range of temperatures.
Reduction of Micro-Defects: Cutting-edge inspection technologies, such as laser scanning and automated vision systems, allow for the detection and correction of microscopic defects that could lead to failures or reduced performance.
Customization for Specific Applications: Improved machining capabilities enable manufacturers to create rotors that are optimized for specific fluids or operating conditions, which is critical for reliability in specialized applications.
Predictive Maintenance: By incorporating sensors during the rotor manufacturing process, smart pumps can be created. These pumps provide data on performance and wear, enabling predictive maintenance and reducing unexpected breakdowns.
Reduction in Vibration and Noise: High-precision rotors lead to a better balance in the pump assembly, minimizing vibration and noise, which are often precursors to mechanical failures.
Adaptive Machining: By incorporating real-time feedback and adaptive control systems in the machining process, variations can be compensated for immediately, leading to more accurate production and, therefore, a more reliable pump.
Continuous improvement and innovation in the machining of screw pump rotors are therefore essential to enhance the performance and reliability of the pumps, which is vital for industries that rely heavily on fluid transfer systems.