
Thread whirling machine XSK-35A
Features:
- The machine is ISO-programmed and easy to operate.
- Milling instead of grinding.
- Machining accuracy reaches international GB/T10089-88 standard or GB/T10227-88 standard 7-6 level and can process high hardness materials.
- The rotating speed of the cutter disc ranges from 3000-8000r/min, realizing high-speed cutting.
- Surface roughness of processed parts can be up to Ra0.8, and Ra0.2 with suitable tools and better performance materials.
- Constant temperature cooling system, and oil mist collection system to ensure a good working environment, to meet the requirements of high-speed cutting.
- Automatic chip removal device, easy to operate, more humane.
- Automatic feeding device, realizing unmanned processing, greatly reducing cost and improving efficiency.
- The outer protection of the machine tool adopts a full protection structure design, convenient operation, safety and reliable.
Thread whirling machine XSK-35A specificities:
This equipment is mainly for small modulus of the long worm shaft type, short worm shaft type, step type and worm sleeve type of different hardness material precision worm.
Batch processing parts accuracy up to GB/T10089-88 standard 7-6 level accuracy, good stability, adaptability, easy to operate with automatic loading and unloading can be realised with one person multi-machine management mode, greatly improving efficiency and reducing costs.
35A-Thread whirling video show
Technical Specifications
Items | Technical parameters | Mark |
---|---|---|
Maximum outer diameter of workpiece | O.D12mm | |
Maximum length of workpiece | 180mm | |
Maximum machining length | 100mm | |
Maximum clamping diameter | C.D25mm | |
Displacement speed X/Z | 6m/min | |
Helix angle adjustment range | £¨+20degree£¬- 3degree£© | |
Milling cutter speed range r/min | 3000-8000r/min | |
Workpiece clamping type | Hydraulic elastic collet | |
Spindle head specification | 25# | |
Repeatability | 0.003mm | |
Surface roughness of machined parts | Ra0.8 | |
Precision of workpiece | Grade7-6 | |
Control system | Taiwan Syntec, Germany Siemens | optional |
Japan Yaskawa servo motor | C/0.85,X/0.85,Z/1.3(KW) | |
Beijing CTB Motor | 5.5KW | |
Oil mist separator | 0.75KW | |
Magnetic chip conveyor | 0.75KW | optional |
Constant temperature controller | 0.75KW | optional |
Tool cooling motor | 0.5KW | |
Long material feeder | 0.45KW | optional |
Total rated power of the machine | 15KW | |
Total machine weight | 2.5T |
Variety of products from customer feedback
In the cutting-edge automotive industry, precision parts are key to enhancing the overall performance and durability of a vehicle. Amongst these components, automotive worms play a pivotal role in the drive system, with their manufacturing precision directly affecting the system’s stability and efficiency. Utilizing a thread whirling machine for the production of automotive worms enables the achievement of exceptionally high machining precision while maintaining efficiency, bringing about a revolutionary improvement in automotive manufacturing.
Â
The thread whirling machine meticulously shapes the worm blank using a high-speed rotating ring of cutting inserts, capable of crafting the complex thread profile of the worm in a single pass. This method significantly surpasses traditional machining in terms of speed, and the surface finish of the worm post-machining is smooth and precise, meeting the strict performance requirements of modern automotive applications.
Â
Moreover, the high customizability of the thread whirling machine allows it to flexibly handle a variety of materials and specifications for worm production. Whether dealing with traditional metal materials or emerging composites, the machine’s carefully programmed operations and cutting tools adeptly manage the task, ensuring each worm meets the highest quality standards.
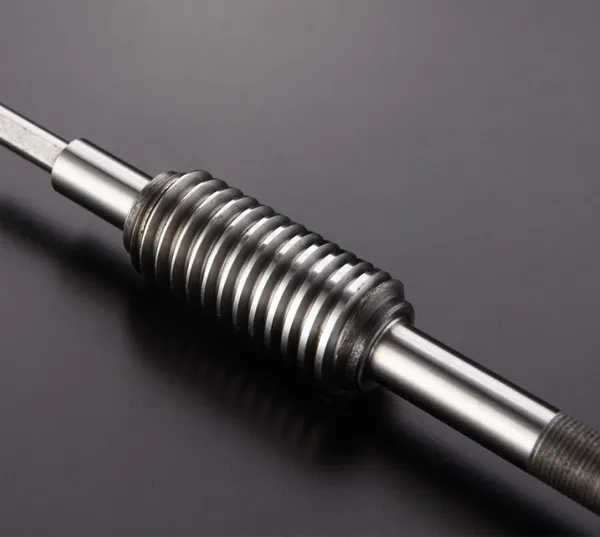
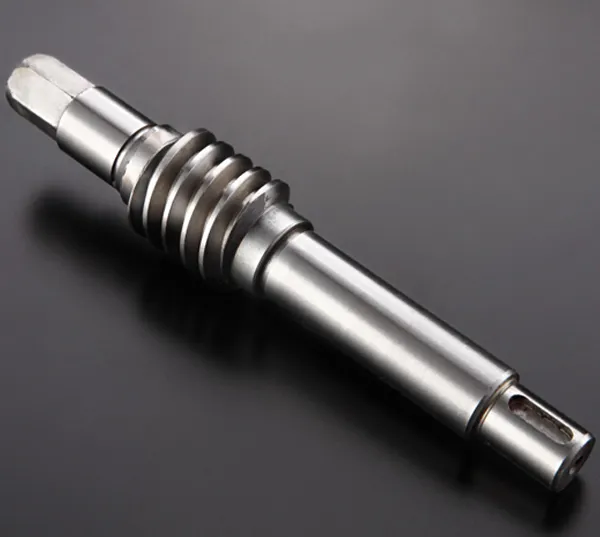
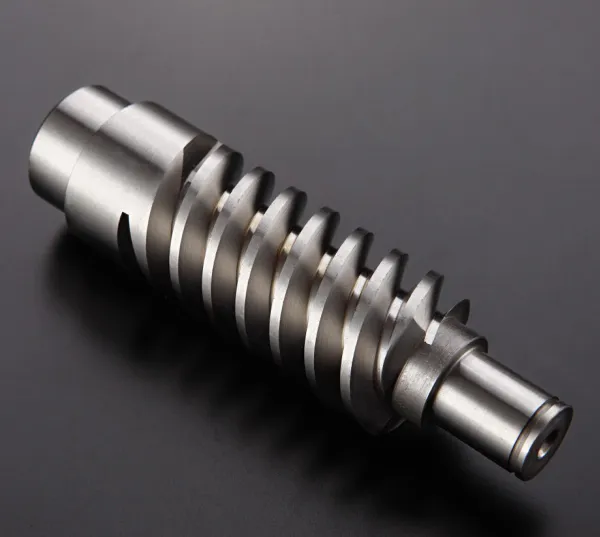
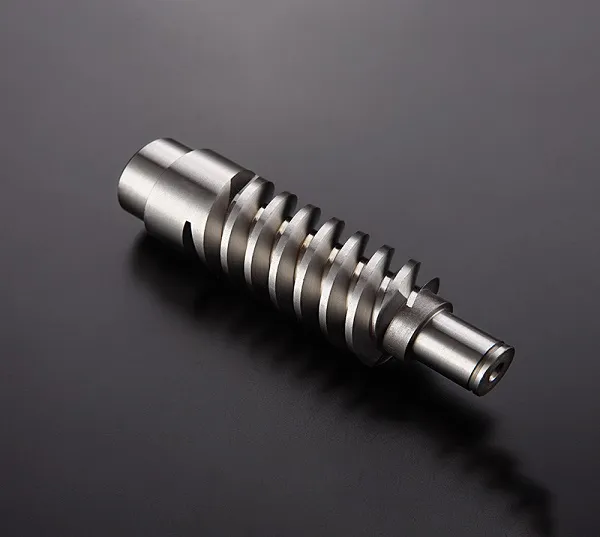
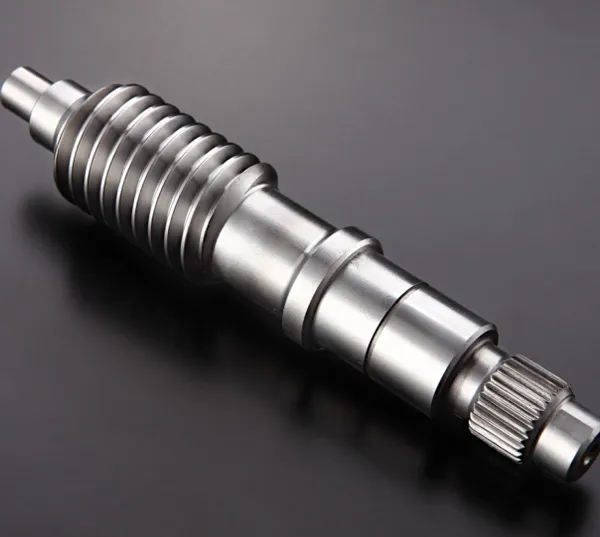
ONMY Thread whirling machine to Start Your Business
Have a look at how some of our clients perceive our goods and services:
Implementing the thread whirling machine in our production line has streamlined our entire manufacturing process. The reduction in manual labor and the machine's high-speed capabilities have drastically cut down on production times. This efficiency boost not only improves our throughput but also allows us to allocate resources more effectively. It's truly transformed our operational efficiency
James AndersonOwner
As a production manager in the automotive industry, efficiency is key. Since incorporating the thread whirling machine into our workflow, we've noticed a significant increase in production speed without sacrificing quality. The machine's ability to produce precise threads at a faster rate has not only improved our output but also reduced downtime significantly. It's an indispensable asset to our manufacturing process.
Christopher TaylorProduction manager
Previous
Next